Hi, i have been reading your discussion because i have similar interests in usage of LFS as henningo. That is simulator for preliminary developing professional racing equipment.
The case is, that we are trying to get on-track DATA in real form without real track driving (racing). That includes noises, track bumps, wind forces and so on. This is why the wheel speeds are so interesting for henningo. He is working on modern traction control system.
TIP to get wind force:
***********************************************************************
This is a math fitting procedure and it is quite accurate. I am using this procedure to define a wind force and homemade dyno correction factor for go-karts and in future on prototype Radical.
Fw....as wind force [N]
A......front surface area [m^2]
Cx....something like drag coefficient [/]
V......speed in [m/s]
ra.....density of air [1,3 kg/m^3]
(1) Fw = A*Cx*V^2*ra/2
As A and Cx are very hard to define it is best to put them both in constant....
C1 = A*Cx [m^2]
(2) Fw = C1*V^2*ra/2
As the engine power diagram is known (kW/RPM) (you should also get it for LFS car) it is possible to determine the force that the car has on the drive wheels.
P…..engine power [kW]
M….engine torque [Nm]
Fe…force of engine on drive wheels [N]
w….engines speed [rad/s] (not RPMs) w = 2*pi*n
i…...transmission [i] including driving gear, primary transmission, differential….
r…..dynamic radius of driving wheels [m]
(3) P = M*w
(4) M = P/w
(5) Fe = P/(w*r)*i
Now that the forces Fe and Fw are on the same level it is possible to write balance equation.
a……acceleration of the car [m/s]
m….mass of the car [kg]
(6) 0 = Fe-Fw–a*m
(7) a = (Fe-Fw)/m
Now it is able to compare cars speed form telemetry (on car or LFS RAF file) and mathematically determined one.
V…. speed of car [m/s]
Vo.. staring speed [m/s]
t….. elapsed time [s]ž
(8) V = Vo+a*t
Compiling equations (2), (5), (7) and (8) results mathematical model for fitting wind force constant C1 (9)
(9) V = Vo+(P/(w*r)*i-C1*V^2*ra/2)/m
Using either hand editing C1 and inspecting graph plot fitting or using one of mathematical fitting methods that are included in LIBs should be just a programming routine from now on.
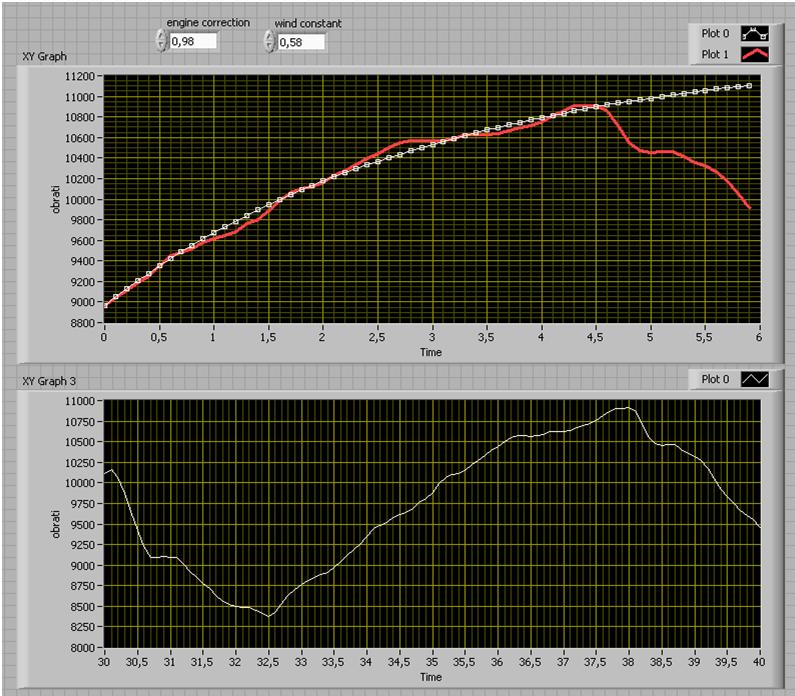
***********************************************************************
I should thank to all of you for hi-level discussion and superb help on the LFS forum.
I prefer LFS as my shelter from ended racing driver career!!!!